If you are interested in some of our products, please feel free to visit our website or contact us for detailed information.
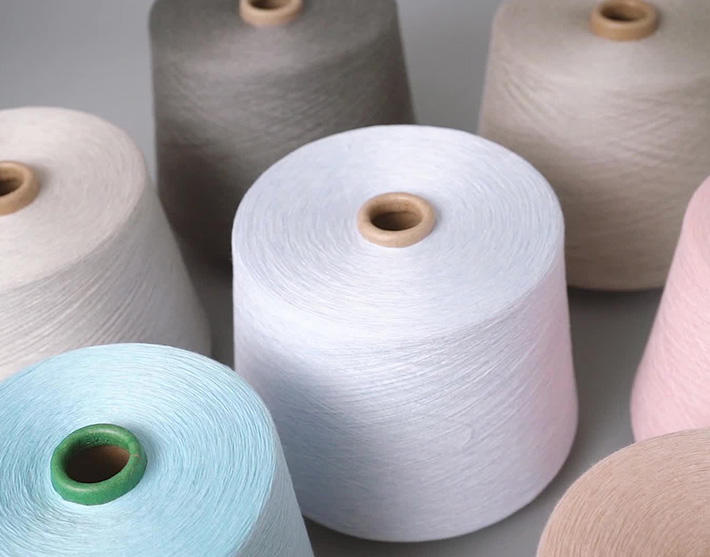
High Stretch Yarns are made from synthetic fibers such as elastane, spandex, or nylon, all of which are known for their exceptional abrasion resistance. Synthetic materials have a smoother surface than natural fibers like cotton, which helps to minimize friction that leads to pilling. This smooth surface reduces the chances of loose fibers detaching, making the fabric more resistant to surface degradation. Some High Stretch Yarns are also designed with microfibers, which are finer and less prone to friction, enhancing their ability to resist wear and tear. These advanced formulations may include treatments that improve the yarn's durability, contributing to its overall resistance to pilling and surface wear.
One of the primary characteristics of High Stretch Yarn is its smooth surface. This is achieved through the careful selection of materials and advanced manufacturing processes that ensure the fibers are as smooth as possible. A smoother surface reduces the friction between fibers when the fabric is subjected to wear, preventing the loosening and breakage of individual fibers that typically result in pilling. The smoothness not only improves the aesthetic longevity of the fabric but also ensures a more durable texture, with less surface abrasion and fewer fibers that can form pills.
High Stretch Yarns are known for their robust tensile strength, which is a crucial factor in their resistance to pilling. When subjected to constant stretching and stress, yarns with higher tensile strength are more resistant to breaking or snapping. The fibers remain intact even after repeated friction, reducing the likelihood of surface degradation or the formation of pills. The enhanced tensile strength also allows the yarn to withstand mechanical forces better, which is particularly important for garments and textiles exposed to dynamic movements or heavy-duty use, like activewear or outdoor gear.
The method of spinning or extrusion significantly influences the yarn's ability to resist pilling. Fine filaments or tightly spun yarns create a denser structure that reduces the possibility of loose fibers escaping, which is often the cause of pilling. Advanced spinning techniques, such as compact spinning or air-jet spinning, can further minimize fiber loss and improve the overall strength and smoothness of the yarn. This leads to a fabric that is more stable under friction and less prone to the formation of pills, maintaining its appearance and functionality for a longer period.
Many High Stretch Yarns undergo polymer treatments or specialized coatings that provide an additional layer of protection against abrasion. These treatments may include silicone-based coatings, polyurethane finishes, or other bonding agents that improve the smoothness of the yarn, enhance its resistance to friction, and prevent individual fibers from loosening. Coated High Stretch Yarns create a barrier that protects the fibers from the mechanical stress of repeated friction, significantly reducing the chances of pilling. These treatments also make the yarn more durable, contributing to the fabric's overall resistance to surface degradation.
The way in which High Stretch Yarns are woven or knitted into fabric also plays a significant role in preventing pilling. A tightly woven or knitted structure helps hold the fibers in place and prevents them from shifting under stress. This ensures that the yarn remains intact despite repeated use, reducing the risk of pilling. A well-constructed fabric also distributes wear more evenly across the surface, which means the stress from friction is spread out, minimizing localized damage. By choosing the appropriate weaving or knitting method, manufacturers can create fabrics that are both durable and resistant to surface degradation.